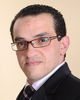
MOHAMED Saad SAAD
Manufacturing and Production Expert
Mokattam, Cairo, EgyptWork Experience
General ManagerFull Time
Dec 2014 - Present -10 yrs, 7 months
- Job Details: Overseeing operations with a particular focus on manufacturing, sales, supply chain, and finance Plan Developing, organizing, implementing, and directing the Company's long and short term strategic plans Driving revenue through strategic business development and to ensure maximum utilization of manpower, materials, machinery to achieve the targeted profitability of the company Advising and implementing manufacturing process improvements to obtain operational efficiency (key skill) Providing technical support to production units from time to time (key skill) Establishing credibility throughout the organization and within the industry as an effective solutions to business challenges Identifying new customers and successfully ensure building the customer base Ensuring timely response to any business inquiries generated Involving in all aspects of Financial Planning, Sourcing of new vendor's, Marketing, Commercial, Production, Quality, merchandising & Man Power, execution and delivery Maintain a deep knowledge of the markets and industry of the company
Factory General ManagerFull Time
Wardatex
Jun 2013 - Dec 2014 -1 yr, 6 months
Egypt , Cairo
- Job Details:- Developing and executing documentation cycle for the new factory and effectively linking and coordinating between the different functional departments. - Balancing the capacities of the different production units to avoid bottle neck points. - Calculating the productivity rates per a labor and equipment through each unit of production phases, hence, the total productivity of a single unit can be calculated that ensure the production flow between consequent phases. - Establishing a planning and following up management efficiently that receives purchasing orders from sales and accordingly sets the necessary plans to meet the sales requirements by the deadlines including (material requirement planning, Production planning and machinery planning). - Establishing an effective warehouse system that efficiently serving the production processes (Raw Material inventory, Spare parts inventory, Accessories and packing material inventory, on process product inventory, finished product inventory). - Developing a quality control system that is covering every process starting from the raw materials, supplies, accessories, on process products up to the finished product. - Ensure planned KPI’s of efficiency and performance are met or exceeded and ensuring that the production is cost effective. - Coordinate, set up and implement standard operating procedures for all production operations. - Making sure that products are produced on time and are of good quality. - Working out the human and material resources needed. - Establish manufacturing priorities and allocate the resources. - Increases management's effectiveness by recruiting, selecting, orienting, training, coaching, counseling, and disciplining managers; communicating values, strategies, and objectives; assigning accountabilities; planning, monitoring, and appraising job results; developing incentives; developing a climate for offering information and opinions. - Develops strategic plan by studying technological and financial opportunities; presenting assumptions; recommending objectives. - Efficiently and effectively organize the company operations to ensure profitability
Project ManagerFull Time
Naturetex (Sekem Group)
Aug 2012 - Jun 2013 -10 months
Egypt , Cairo
- Job Details:Conducting a project and manage its entire development process from start to end. Creating a full-fledged project plan that clearly explains the details of projects, technical information and financial implications. Deciding the scope of projects, goals to be achieved and expected deliverables together with company management and other stakeholders. Estimating and assembling a project team as well as coordinating the activities of the teams. Estimating the budget for the entire project and for each level of accomplishment. Submitting budget proposals to management and making amendments when necessary. Effectively communicate the project scope, milestones and deliverables to project team and stakeholders. Build, maintain and grow relevant business associations or relationship necessary for achieving success in the project. Proactively anticipate potential crises, devise contingency plans and manage changes in the project scope. Facilitating the planning, structuring and implementation of the entire project Tracking individual deliverables as well as providing feedbacks and quality control on projects. Manage the budget of the project as well as the allocation of various resources. Setting milestones, timelines and deciding the scope of each deliverable Providing consistent support to the project team and ensuring the direction of the project’s execution is followed. Monitoring and reporting of project’s progress (progress, challenges and solutions) to all the stakeholders that need to know. Appraising the project and assessing the results achieved plus writing of recommendations report after every project.
Factories ManagerFull Time
Carinawear & Solotex
Mar 2001 - Jun 2012 -11 yrs, 3 months
Egypt , Cairo
- Job Details:Highlights: - Defined project tasks and resource requirements, led the development of project plans and expanded production units from 7 machines for Carina factory and 14 for Solotex to 86 Machines and 128 machines respectively. - Initiated the productivity computation system which calculates the productivity of each labor, resulting in increased productivity, decline in absenteeism and motivated workforce. - Conceptualized a new system for Inventory stocks, Sales, and goods on process that significantly secure correct inventory stocks, supported sales, reduced lost sales and guaranteed just in time delivery. Key Responsibilities: - Planning, Formulating, organizing, controlling and directing production activities in addition to managing the functional areas of Planning, Quality Control, warehouses, Purchases, supplier and client management, hiring workers, Supervisors, and Department heads. - Managing time-lines and work priorities and allocating resources to meet the assigned factory time-lines and goals of 2 factories Carina and Solotex. - Computing operational and maintenance cost estimates. Devising section budgets, and effecting cost cutting measures to maintain adherence to the same. - Supervising and managing the staff and equipment/machine throughout the production process. - Ensuring that product effectively satisfies the quality level ordered by the customer through the quality control team. - Enabling proper utilization of resources and ensured there is no wastage. Monitoring labors productivity in every phase of production process. - Tracing issues which hold up productivity and monitoring the efficiency of all organization departments, ensuring achievement of every department objectives that secure the achievement the entire organizational objectives. - Collaborating with sales agents, vendors and financial department to ensure the successful run of receiving and shipping schedule. - Reviewing the overall performance.
Education
MBA in General Management
Arab Academy for Science, Technology and Maritime Transport (AAST)Jan 2010 - Jan 2012 - 2 yr
BA in Textile Engineering
Helwan UniversityJan 1990 - Jan 1995 - 5 yr
High School - Thanaweya Amma
Minia Secondary Military SchoolJan 1990
Skills
- Planning
- Production Management
- Problem Solving
- Motivating
- Quality Control
- Warehousing
- Manufacturing & Production
- Quality Control
- Textile Engineering
- Production Development
View More
Languages
Arabic
FluentEnglish
Advanced
Training & Certifications
MBA
Arab Academy For Science And Technology And Maritime Transport·2012