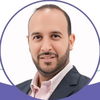
Islam Adel Kassem
Engineering, Facilities, Director, operation, Corporate Real Estate, Project
Sheikh Zayed, Giza, EgyptWork Experience
Executive Manager, Campus ServicesFull Time
ESLSCA University
Dec 2023 - Present -1 yr, 6 months
Egypt , Giza
- Job Details:- Established the Campus Services Department with structured mission, vision, org chart, and operational framework aligned with institutional goals. - Generated new revenue through catering partnerships, optimized event budgeting, and improved vendor cost control. - Developed and implemented full Health & Safety protocols, including an evacuation plan, campus-wide fire extinguisher rollout, and staff training. (25+ incident-free events). - Directed facilities operations and renovations, achieving cost savings of EGP 300K (10.7%) via value engineering on a major studio project. - Launched university-wide employee transportation and parking systems, improving mobility and reducing traffic congestion. - Executed space optimization initiatives accommodating a 25% staff increase with minimal cost, and delivered a complete asset inventory and seating plan. - Coordinated high-level campus logistics and VIP visits, receiving formal recognition from senior leadership.
Head of Real Estate, Facilities & AdminFull Time
- Job Details:As per my resume
Facilities Management ConsultantFreelance / Project
Freelance
Sep 2022 - Present -2 yrs, 9 months
Egypt , Giza
- Job Details:As per my Resume
Regional Facilities Services & Real Estate Leader MEAFull Time
Corteva Agriscience
Aug 2019 - Aug 2022 -3 yrs
Egypt , Cairo
- Job Details:Roles & Responsibilities: - Ensure all Sites well maintained, providing an excellent working environment for occupants. - Determine the type of services & SLAs to be provided for each site and execute it effectively. - Utilize common systems to manage works and track costs to maintain sites, while meeting OPEX & CAPEX requirements. - Ensure Site’s Capital assets are maintained & working safely.
Education
Project Management - PRMG in Project Management
American University in Cairo (AUC)Jan 2011 - Jan 2012 - 1 Year
BSc in Mechanical Power Engineering
Ain Shams University (ASU)Jan 2000 - Jan 2005 - 5 yr
High School - Thanaweya Amma
The English SchoolJan 2000
Achievements
Strategic Facilities, Project Management & Operations Executive with 15+ years of experience driving operational excellence across automotive, manufacturing, IT, education, and agriculture across leading organizations like General Motors, HSBC, IBM, Corteva, British Council, and ESLSCA University. I’ve built my career transforming facilities operations into engines of efficiency, safety, and strategic growth through leading cross-functional teams (100+ staff), optimizing real estate portfolios (20+ sites), completing $2M+ facility projects on time and under budget and delivering 15-25% cost savings through tech-driven FM solutions. From managing numerous commercial buildings to overseeing regional FM portfolios across MEA, my work centers on aligning facilities strategy with business goals—through cost control, energy efficiency, stakeholder engagement, and future-ready infrastructure.
Skills
- Mechanical Engineering
- Business Management
- Security
- Communication skills
- Problem Solving
- Mechanical
- Engineering
- Project Management
- Microsoft Project
- Manufacturing
Languages
English
FluentArabic
FluentFrench
Intermediate
Training & Certifications
Managing Technology & Innovation: How to deal with disruptive change
EDX·2021FMP Certificate
IFMA·2021PMP Project Management Proffesionals
PMI (Project Management Institute)·2018Training on IBM Account Management
Bilfinger COC Germany·2016Labor Law
Top Business·2015Project Management Professionals (PMP) Exam Preparation Course
AmCham ·2013Effective Communication Skills
Dale Carnegie Training·2012Project Management (PRMG)
American University in Cairo (AUC)·2012IBM MAXIMO – Asset Management Implementation Training Course
HP Enterprise·2010Wonder-Ware SCADA system interface Level I
Rockwell Automation (Amsol)·2010PLC controller (Allen Bradley) and Troubleshooting analysis Level I,II,III
Rockwell Automation (Amsol)·2010Creative Problem Solving & Decision Making Course
SCITRON·2010Integrated Management System Awareness & Internal Auditor Course
Quench·2010Accident Investigation Course
Dubai Integrated Safety Solutions DISSC·2010Time & Stress Management
LOGIC consulting·2010Statistical Engineering RED-X Apprentice
General Motors Egypt GM·2010Business Simulation
CELEMI Decision Base·2009OHSAS 18001:2007 & ISO 19011:2002 Management System Internal Auditor
Quench·2009Business Finance for non-Finance
CELEMI Apples and Oranges·2009OHSAS 18001:2007 Occupational Health & Safety Management System
American University in Cairo AUC·2009Using Statistical Techniques for Decision making & Quality Improvement
American University in Cairo AUC·2008Management Course (problem Solving)
Saudi Arabian Airlines·2007Emergency and Evacuation Planning workshop
International Safety Council·2006Safety regulations in Cairo Airport Course
Cairo Airport ·2006Hygiene and HACCP Course
SGS·2005Training in Engineering Department
Concorde –El Salam hotel·2004