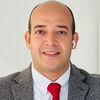
walid gomaa ahmed
Material management,production,inventory
6th of October, Giza, EgyptWork Experience
Supply chain Section HeadFull Time
Sinai Cement - VICAT GROUP
Oct 2020 - Present -4 yrs, 9 months
Egypt , Giza
Procurement / Warehouse Section headFull Time
Building Materials Industry Company
Nov 2017 - Oct 2020 -2 yrs, 11 months
Egypt , Giza
- Job Details:• Negotiate with suppliers to create the best deals. Handling all raw materials needed for the operation (Gypsum-Sand- Serpent tint- mazout-Bags-Clay-Iron Ore …. ) in time • Handling the vendor payment according to the plane with priorities. • Manage a team of buyers /runners (giving assignments and tasks, monitor progress to ensure objectives are met . • Negotiate to find best deal/contract to serve the plant with martials with ideal condition, and avoid any stoppage could be happen due to any shortage. • Find alternatives supplier for each material. • Generating reports in SAP and MS-EXCEL for the Purchase requisitions, RFQ’s and PO’s; • Monitoring of the Document control and expediting activities concerning the above purchasing documents; • Attending vendor facilities, as necessary in expediting and follow-up • Generating vendor database for the materials and services; • Vendor evaluation.. • Convert all imported POs to be fabricated locally.
Material Management section HeadFull Time
FLSmidth - Egypt
Jun 2012 - Oct 2017 -5 yrs, 4 months
Egypt
- Job Details:• Manage the All processes Maintenance and Engineering Activities. • Familiar with ERP System (Maximo) • Spare Parts studies (Strategic, consumable ,…….etc. ) for production equipment • Maintain physical condition of warehouse by planning & implementing new design layouts; inspect equipment; issue work orders for repair & requisitions. • To provide the required resources for the maintenance teams in performing their jobs from human and material aspects as well. • To ensure the effective planning, implementation, Cost tracking, Cost Control within Budget, record keeping and auditing of corrective and preventive maintenance activities. • To assign the spare parts stocking policy through developing methods of parts supplying in achieving minimum stock turnover performance indicator. • To report on the maintenance and operation activities and performing data analysis to help the Works Director in monitoring the progressing and/or retarding of maintenance activities utilizing key performance indicators. • To issue and follow-up the purchase requests and fabrication orders as well. • To perform the reverse engineering activities for the parts to be fabricated. • To enhance the reporting functionality of the computerized maintenance management system currently implemented in the plant by improving the quality of data and proper new data feeding "MAXIMO designed by IBM".
Education
Bachelor's Degree in Mechanical Engineering
Benha UniversityJan 2004 - Jan 2008 - 4 yr
High School - Thanaweya Amma
Ahmed LoftyJan 2003
Achievements
I have a multinational experiences with high skills related to inventory , warehouse and supply chain . also i am directed with financial target with top management vision to score high KPIs , i participated in many projects related to cost saving and we already saved 20 Million by managing the obsolete items and sharing with other plants - with purchasing foreign spares locally
Skills
Languages
Arabic
FluentEnglish
Advanced
Training & Certifications
Understand the key guidance of CSR and Sustainable Procurement
2022Certificate by subsidy Export
2022New customs clearance regulations Certificate - The French Chamber of Commerce and Industry in Egypt.
Chamber of commerce·2022CISCM - certified international supply chain manager
IPSCMI·2020Six Sigma
2015Supply Chain
2015}onstruction industries
ORASCOM construction industries·2007Maintenances pumps, compressors and turbines
Coke and chemicals company -HELWAN·2006