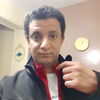
EL Amir Hassan Allam
Senior procurement and sourcing manager
Mohandessin, Giza, EgyptWork Experience
Procurement DirectorFull Time
Hassan allam -manufacturing sector
Feb 2021 - Mar 2025 -4 yrs, 1 month
Egypt , Cairo
Education
Master degree in Business administrative in Operation supply chain management
Colorado Technical UniversityJan 2008 - Jan 2010 - 2 yr
bsc in commerce in Accountancy
Cairo University (CU)Jan 1992 - Jan 1997 - 5 yr
Skills
- Microsof
- ERP
- Microsoft Excel
- Hard Skills
- Supply Chain
- Microsoft Word
- Supply Chain
- Purchasing Management
- Inventory Control
- Forcasting the demands number
View More
Languages
English
FluentArabic
FluentGerman
Advanced
Training & Certifications
Advanced Professional Certificate in Procurement & Supply chain Manager leading to Chartered Procurement & Supply chain Manager
Endorsed by American Association for Operations Management. Through American Chamber Of Commerce in Cairo ·2016tranining cource in Commercial services management
ASEC ·2012