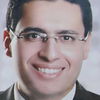
Amr Mohamed Moharram
Supply Chain Manager at Ultimate Pharma
Moharam Bek, Alexandria, EgyptWork Experience
Supply Chain ManagerFull Time
Ultimate Pharma
Nov 2019 - Present -5 yrs, 8 months
Egypt , Alexandria
- Job Details:Main responsibility: managing supply chain duties (planning, foreign & local purchasing, warehousing, logistics), developing the overall department policy & procedure and correlation with other departments (regulatory affairs, R&D, production, Q.C & Q.A, sales & marketing, finance & custom brokers). I-Planning duties: 1- Study the sales forecast taking into consideration the available lines capacity and the available stocks of finished goods and raw & Packaging materials in order to: a- Set plans for production (monthly & weekly). b- Set plans of material supply meeting production needs & available budget. 2- Place purchase orders accordingly to ensure orders / supplies are in line with the production plan. 3- Analyze days of supply on hand. 4- Setting a re-order amount for each item depending on production plan & capacity and item lead time. 5- Preparation of B.O.M (Bill Of Materials) depending on product master formulae and batch sizes. 6- Insure proper alignment of the planned purchasing orders taking into consideration the minimum order quantities & lead time. 7- Preparation of the yearly import plan to be introduced to the Egyptian drug authority. 8- Responsible for coordinating any toll manufacturing by submitting / receiving all kind of information between the company and the client (either toll in or toll out). 9- Issue a quarterly report showing the actual production versus sales forecast. 10- Review and suggest ways to improve the current flow process and stock rotations. II-Purchasing duties: 1- Manages the local and foreign purchasing cycles for the company which includes the following steps: a- Receiving the purchase requests of the needed item(s) either from the planning department or from other sectors. b- Selection from available suppliers for the needed item, receiving the quotations (3 quotations should be available), bargain for best prices and purchasing terms in order to select the best offer based on item approval from the authorized personnel, price and purchasing terms. c- Budgeting request from finance. d- Issuing the P.O (Purchase Order) and its approval. e- Sending the P.O to the supplier and follow up item arrival/receive with him. f- After item receive, follow up of item approval from the authorized department. g- Based on item approval, follow up of supplier payment according to the approved P.O. 2- Follow up the preparation of supplier list for each category (engineering, laboratory, general, specialized, raw/ packaging materials) including: item code, item name, supplier (company/ group) name, contact person, contact person Mobile number and e-mail. 3- Arrangement of vendor contracts when needed. 4- Continuous supplier sourcing based upon purchased goods quality analysis and cost. 5- Open orders follow up. 6- In foreign purchasing operations, close follow up of the foreign-purchased items clearance after their arrival to the final destination with the custom brokers. III-Warehousing duties: 1- Managing the warehousing cycle including: A- For raw materials: a- Receiving the starting material from the supplier and store it in the dedicated quarantine area for starting material. 2- Follow up of the approval of starting material by Q.C and transfer them to the approved items area. 3- Dispenses the required starting materials for production after receiving of a signed order of the authorized person according to FIFO (First In First Out). 4- Receives the returned items from production with return order signed from authorized person. 5- Strict stock supervision and documentation of added/ dispensed/ returned items so as the real stock is usually equal to the documented stock. 6- Strict supervision of locations so as the real location contains same items (identity and quantity) of the documented one. 7- Balance calibration, temperature and humidity check… etc upon quality agreement. B- For finished goods: a- Receive the finished product from production and store it in the dedicated quarantine area for finished product. b- Follow up of the release of finished goods by Q.A department and transfer them to the approved items area. c- Provides the needed finished product for sale after receiving of a signed order from the authorized person according to FEFO (First Expiry First Out). d- Receives the returned goods from sales with return order signed from authorized person and take a decision about them in cooperation with quality departments. e- Strict stock supervision and documentation of finished goods so as the real stock is usually equal to the documented stock. f- Strict supervision of locations so as the real location contains same items (identity and quantity) of the documented one. 2- Providing available stock locations data for planning and purchasing departments. 3- Analyze slow moving and obsolete inventory and issue relevant reports. IV-Logistics: 1- Arranging the contract of suitable logistic company (in order to transfer the finished goods from the company to the cli
Planning ManagerFull Time
Fipco (El Fath for pharmaceutical products and cosmetics)
Jan 2018 - Nov 2019 -1 yr, 10 months
Egypt , Alexandria
- Job Details:Main responsibility: coordination between company departments and forecasting future. Duties: 1- Receive the yearly / quarterly sales forecast; also receive the export yearly forecast. 2- Study the sales forecast taking into consideration the available lines capacity and the available stocks of finished goods and raw & Packaging materials. 3- Set plans for production and for materials supply. 4- Place purchase orders accordingly to ensure orders / supplies are in line with the production plan. 5- Analyze days of supply on hand. 6- Insure proper alignment of the planned purchasing orders taking into consideration the minimum order quantities, lead time, …..etc. 7- Coordinate the new products launches process by working closely with Marketing, Production, R&D, & Purchasing.. 8- Responsible for coordinating any toll manufacturing by submitting / receiving all kind of information between the company and the client. 9- Follow-up on all production lines ensuring the production is following the preset production plan. 10- Conduct regular meetings with production / sales to address all open issues. 11 Follow-up regularly on the other department (Q.C. for under inspection items, Purchasing for open P.O.& BOM, Warehouse for storage capacity ..etc ). 12- Issue a quarterly report showing the actual production versus sales forecast. 13- Analyze slow moving and obsolete inventory and issue relevant reports. 14- Review and suggest ways to improve the current flow process 15- Investigate root cause for unfavorable trends; implement corrective actions where appropriate. 16- Manages the local purchasing cycle for the company. 17- Develops department policy and procedure. 18- Arranges vendor contracts, bargains for best costs, and observes quality of the purchased materials. 19- Selects supply sources based upon analysis.
Deputy of production managerFull Time
Fipco (El Fath)
Apr 2017 - Jan 2018 -9 months
Egypt , Alexandria
- Job Details:Main responsibility: To ensure the quality of products & plan management according to GMP rules in all company production departments (I.V infusions, ampoules and drops, Haemodialysis solutions, Purified water, sodium bicarbonate sachets). Duties:(under the supervision of the general production manager) 1- Preparing, revising and updating SOPs for all production departments to bring efficiency improve and achieve maximum cost savings. 2- Leading the production team to carry the production activities and achieve targets. 3- Preparation and implementation of GMP related documents and monitoring of cGMP aspects in the production area. 4- Ensuring that all production equipment are maintained in good working manner. 5- Ensuring conformance of manufacturing processes with organizational objectives and policies. 6- Fulfilling the monthly and weekly production plans according to the schedule. 7- Training of the production employee, employee were well trained on: a- on job training. b- cGMP rules. c- Contaminants of the production area, their monitoring and how to prevent them. d- Gowning procedure. e- Documentation practice. f- water treatment plants (purified and WFI) functions. 8- Since September 2018, I was charged to fulfill planning duties in addition to my production ones.
Production coordinator and supply chain executiveFull Time
- Job Details:Main responsibility as production coordinator: To ensure that manufacturing processes at other manufacturing sites is done in accordance to the MOH quality aspects in order to assure products quality. Duties: 1- Coordination between company and manufacturing sites. 2-Troubleshoots and resolves operations issues. 3-Work to ensure maximize product reliability and minimize costs and loss. 4- Planning for production campaigns. 5-Delivery of raw and packaging materials to manufacturing sites. 6-Planning and executing pilot batches production in manufacturing sites. 7-Planning and executing commercial batches production in manufacturing sites. 8- Coordination of samples withdrawal from manufacturing sites. 9-Coordination with bio-equivalence canters to carry out bio-equivalence studies. 10-Acting as contact point between company R&D department and manufacturing sites. 11- Coordination of contracts issuing between the MOH and manufacturing sites. 12-Revision and approval of artworks in coordination with manufacturing sites. Main responsibility as supply chain executive: To manage & execute supply chain operations. Duties: 1-Preparation of supply plan according to forecast and available budget. 2- Revision & approval of Purchasing orders. 3- Revision & approval of delivery notes. 4- Revision & approval of purchasing invoices. 5- Contact of suppliers when needed. 2- Ampoules Production Department Manager in Pharco Pharmaceuticals (31st km, Alexandria-Cairo desert road) (May 2015- November 2016) Main Responsibility: To ensure the quality of products & plan management according to GMP rules in the ampoules production department. Duties: To insure the implementation of the following: 1- Utilization of the annual, monthly, weekly & daily management. 2- Planning work schedule in the department and following up with the needs to achieve the plan. 3- Facilitating the production process. 4- Training of employees in the department. 5- Organizing the employees to facilitate the production process and achieve the target plan. 6- Handling the production process to solve any related problems. 7- Correlation with other departments to solve any related problems. 8- In-process control. 9- Preparing & checking documents and work instructions. 10- Internal Auditing. 11- Complaints/Recalls handling. 12- Deviation Handling.
Education
Bachelor in Pharmaceutical
Alexandria University (ALEXU)Jan 2000 - Jan 2005 - 5 yr
High School - Thanaweya Amma
Saint MarcJan 2000
Achievements
Accomplishments: 1- Program of managerial skills – 1 to 3/ 2014- Pharco training. 2- Microbiology Diploma- 2016- HIPH (Hugh institute of Public Health in Alexandria). 3- Supply Chain principles- 10/2020- Georgia Institute of technology- USA 4- Six Sigma Green Belt- 10/2020- Georgia University- USA 5- On going MBA course
Skills
- Leadership
- Sterile and non sterile dosage forms preparation
- Toll Manufacturing
- CGMP
- Process Management
- Decision Making
- Production scheduling
- Quality Management
- Quality Management System
- Planning
View More
Training & Certifications
Production planning
Mega Com·2018conflict management
Pharco·2016Crisis Management
Arab Academy for Science, Technology & Maritime Transport·2016Problem solving and decision making
AFAQ Misr·2015Program of managerial skills
Pharco·2014Basic of planning skills
Pharco·2012Negotiation & good deals
Pharco·2012Managerial Skills Improvement
Pharco·2009