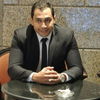
ALSHAERIF AHMED EL MARGHANY
R&D and Quality Head at Mashreq for Business Development- Unilever Mashreq Group
6th of October, Giza, EgyptWork Experience
R&D and Quality HeadFull Time
Mashreq for Business Development- Unilever Mashreq Group
Dec 2019 - Present -5 yrs, 7 months
Egypt , Alexandria
- Job Details:As per mentioned in my CV
FC&A Deputy Technical Support DirectorFull Time
- Job Details:To demonstrate the use and benefit of our flavors in food and beverage products to achieve sales targets and customer requirements. - Assist in developing innovative new products and concepts for flavor application -To prepare flavor samples to be sent to customers to evaluate them in his production lines or in his applications - Work with Flavorist to create spray dried flavors and flavor solutions for customer projects. Job responsibilities: ▪ Evaluate flavors in food and beverage applications ▪ Pro-actively monitor flavor performance and stability in food products ▪ Select optimal flavours for customer projects according to all relevant requirements (taste profile, legislation, technical suitability, costs, etc.) ▪ Act as responsible project owner or leader for all allocated projects. ▪ Collaborate with cross-functional teams to develop and execute customer growth opportunities. ▪ Arrange and conduct tasting sessions, process and interpret the results. ▪ Present flavours and flavoured food products to customers to evaluate the flavor and working with R&D teams of the customer to implement the trails of the flvs into their applications. ▪ Provide support and exchange information on flavour performance, food recipes, etc. with other Givaudan sites. ▪ Work strictly according to the company requirements for optimal safety, hygiene and protection of the environment. ▪ Supervising Spray Dry productions by third party during whole process of the spry drying. ▪ Produce prototype samples for projects; prepare Lab and QC reference samples ▪ Ensure flavour samples are aligned with the regulatory (correctly labelled and flavour submissions receive lot numbers. ▪ supervision receiving/controlling raw materials and control stocks in Laboratory through FC&A subordinates. ▪ Maintain a clean and orderly laboratory environment in accordance with EH&S guidelines and good laboratory practices. ▪ follow up dispatching samples on a timely basis as per part of customer satisfaction management. ▪ Basic knowledge of food technology and raw materials (necessary toadhere to safety guidelines) ▪ Demonstrates skills to prepare for and assist with flavour systems or product evaluations as well as various Sensory Tests. ▪ Acute sense of smell and taste. ▪ Lab experience and experience in handling with chemical substances, preferable spray dry manufacturing experience. ▪ New product industrialization and scaling-up until production can take over responsibility using the support of the flavorists. Identify and implement improvements projects to initiate a new idea to be presented to our customer or to re-evaluate the existing products to enhance the characteristics of the flavor or make a cost savings to decrease the cost and achieve more profits. ▪ Administratively introduces new formulations to the manufacturing site, incl. Formula conformity checks ▪ Provide support to Improve quality consistency of production processes & support the quality assessment process for new flavor ingredients. ▪ Provide support in solving internal and external complaint including the usage of rejected production or raw materials.
Quality Control & Food Safety ManagerFull Time
- Job Details:Manage and develop the application of quality systems and food safety ISO 9001 - ISO 22000 – HACCP - GMP – ISO 18001. • Devising and establishing a company's quality procedures, standards and specifications; • Reviewing customer requirements and making sure they are met; • Working with purchasing staff to establish quality requirements from external suppliers; • Setting standards for quality as well as health and safety; • Making sure that manufacturing or production processes meet international and national standards; • Looking at ways to reduce waste, increase efficiency , process & methods capabilities, • Setting up and maintaining controls and documentation procedures; • Monitoring performance by gathering relevant data and producing statistical reports; • Making suggestions for changes and improvements and how to implement them; • Using relevant quality tools and making sure managers and other staff understand how to improve the business; • Making sure the company is working as effectively as possible to keep up with competitors. • Working with the Marketing team on any new launch Projects from the starting of the designing till the go live of the Project. • Working with the Warehouse Team to improve and development the storing Systems and the Warehousing Methods to insure that the Storage Conditions are Excellent for the different Raw Materials. • Making sure that manufacturing or production processes meet the ideal Standards & Specifications • Defining & managing the quality procedures in Cooperation with the operational staff and other departments then setting up and maintaining controls and documentation procedures. • Monitoring performance by gathering relevant data and producing statistical reports • Ensure a high level of internal and external customer service. Investigate (and correct) customer issues and complaints relating to quality. • Managing and following up Quality staff and Production workers engaged in inspection and testing activities to ensure high productivity and high technical integrity. • Coordinate objectives with production procedures in cooperation with the Operations Director to maximize product reliability and minimize costs & wastes. • Interact with vendors to ensure quality of all purchased Materials – Plus Making the Supplier Audit to ensure the Process. • Design, develop and implement quality control training programs for the Quality Team besides I’m a soft skills trainer for the others employees & departments.
SAP Supporting Specialist + Quality & In Process Control Supervisor.Full Time
- Job Details:• Data Cleansing Coordinator (DCC) member in the deployment local team of the outlook Project ( SAP ) . • Power User (PU) member in the Implementation team of the SAP Project. • Responsible for training the END USER (EU) about the Quality Control and Operations Process of the SAP System . • A member with the Global Implementation team in the Testing Team who are responsible for implementing and running the OUTLOOK Project (SAP) in Givaudan EGYPT. • One of the Local Supporting Team after Go-Live to Support any streams for any Departments in any technical issue related to SAP. • Managing and supervising a team of 4 Quality Control Analysts & member in the Operation committee with 4 Production Engineers and the RIM Specialist. • Responsible for product Quality Planning for all products, raw materials & finishing supplies. • Supervising & ensuring the implementation of the Manufacturing standards & procedures. • Ensuring that all the materials used are in adherence with the company specifications. • Responsible for the compilation of Quality Plans & Quality Control Plans/Inspection & test plans. • Improving & maintaining quality standards through laboratory analysis & quality inspections & also by conducting calibration programs for all the laboratory instruments. • Developing a sampling library for the raw materials & finished products. • Updating the Quality Control Database by all the Raw Materials & finished products specifications. • Preparing & standardizing the volumetric & test solutions to maintain quality standards. • Ensuring the adherence of all the production operators & machines to the Quality standards & hygienic rules. • Perform all the Microbiological tests of all the received Raw Materials & finished products. • Responsible for monitoring the hygienic condition of the site by doing Swab Tests and reporting to the operations management staff. • Monitoring the microbiological safety of the manufacturing environment. • Following up on the product delivery & delivery reports. • Minimize the wastage during the production process. • Implementing systems such as GMP, HACCP, SHE & 5S.. • Preparing the department annual budget.
Education
Technical Diploma in Quality Management
ASI ( American Supplies Institute )Jan 2015 - Jan 2016 - 1 Year
BSc of Agriculture Science in Plant Protection Sciences
Cairo University (CU)Jan 2002 - Jan 2006 - 4 yr
High School - Thanaweya Amma
الإبراهيمية الثانوية بنينJan 2001
Achievements
Senorita for Food Industries – Americana Egypt Group •Infra-Structure Development : •Increase the number of the QC labs from 1 lab only to be 5 specific labs serves the different sectors of the Quality Department •These 5 labs had been prepared regarding to the highly grade of GPMs / food safety / safety requirements. •All the labs are provided with the last updated versions of the laboratories technology. •All the tests and the different attributes are making full automated. •People Development : •Implemented the Competence Matrix for the People (KEESA). •Making annual plans to develop and improve the QC Team (Technical & Soft Skills). •Implement the Delegations Management. •Encourage the People to develop their selves educationally (TQM / MSC). •Implement the PDR system to set a goals and strategies to be achieved frequency which is increase the performance of the people. •Implement the Weak Links System which is monitoring the weak points.
Languages
Arabic
FluentEnglish
Advanced
Training & Certifications
CMQ - Certified Manager of Quality
American Supplies Institute - ASI ·2016Lead Auditor ISO 22000
AAST·2015TQM - Total Quality Management
AUC - American University at Cairo·2014