Find the Best Jobs in Egypt
Searching for vacancies & career opportunities? WUZZUF helps you in your job search in Egypt
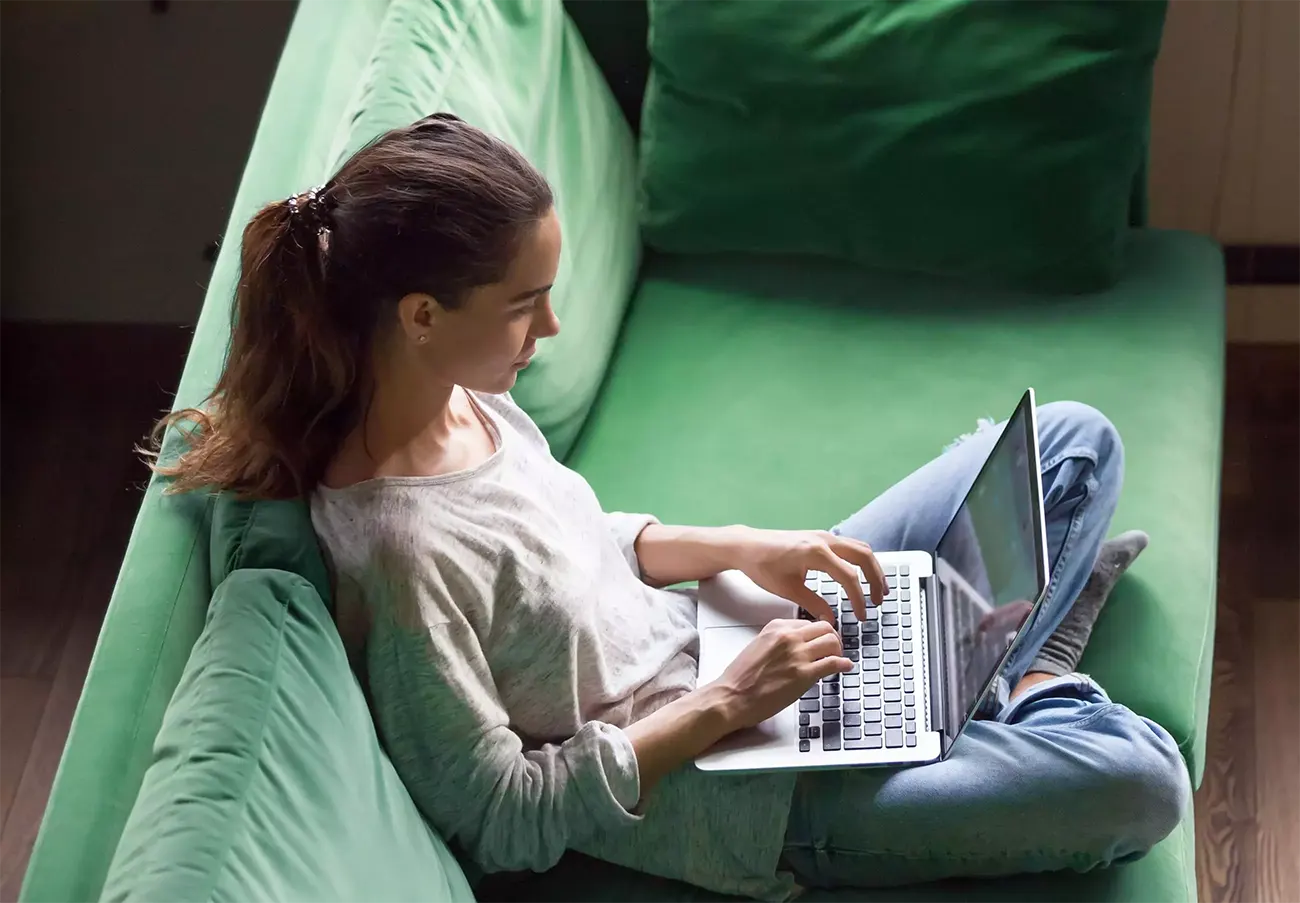
Join Egypt's Top Companies
Latest Jobs
- Call Center Agent B1+ ( English Speakers ) - GradsEtisalat Egyp... - Cairo3 hours ago
- Backoffice (Mail&Chat) Excellent English SpeakersEtisalat Egyp... - Cairo2 hours ago
- Doctor / pharmacist/ Dentist / Dermatologist : female onlyLa Parisienne... - Cairo2 hours ago
- Mail&chat (Excellent English speakers ) backoffice,e&UAE GraduatesEtisalat Egyp... - Cairo2 hours ago
- Non-Voice Account |Chat & E-mails|Excellent English Speakers| e&UAE.Etisalat Egyp... - Cairo1 hour ago
- Head CashierDancinggoat - Giza1 hour ago
- Senior UI/UX DesignerRahala - Giza1 hour ago
- Chefneom pyramids... - Giza12 minutes ago
Browse Jobs by Career Level
Browse Jobs by Category
- Accounting/Finance JobsFinancial Manager JobsInternal Audit JobsTreasury Manager Jobs
- Administration JobsSecretary JobsOffice Manager JobsReceptionist Jobs
- C-Level Executive/GM/Director JobsGeneral Manager JobsChief Executive Officer JobsChief Financial Officer Jobs
- Creative/Design/Art JobsGraphic Design JobsUI/UX Designer JobsInterior Design Jobs
- Customer Service/Support JobsCall Center JobsAccount Executive JobsTour Operator Jobs
- Education/Teaching JobsEnglish Teacher JobsScience Teacher JobsArt Teacher Jobs
- Engineering - Construction/Civil/Architecture JobsTechnical Office Engineer JobsSite Engineer JobsPlanning Engineer Jobs
- Engineering - Mechanical/Electrical JobsMechanical Engineer JobsElectrical Engineer JobsProduction Engineer Jobs
- Engineering - Other JobsBiomedical Engineer JobsSales Engineer JobsAgricultural Engineer Jobs
- Engineering - Telecom/Technology JobsSoftware Engineer JobsNetwork Engineer JobsPre-Sales Engineer Jobs
- Hospitality/Hotels/Food Services JobsRestaurant Manager JobsFood & Beverage JobsExecutive Chef Jobs
- Human Resources JobsRecruitment Specialist JobsPayroll Specialist JobsPersonnel Specialist Jobs
- IT/Software Development JobsWeb Development JobsFront-End Development JobsAndroid Jobs
- Installation/Maintenance/Repair JobsIT Specialist JobsMaintenance Engineer JobsTechnical Support Specialist Jobs
- Legal JobsLawyer JobsCorporate Lawyer JobsSecurity Manager Jobs
- Logistics/Supply Chain JobsWarehouse JobsExport Manager JobsPurchasing Specialist Jobs
- Marketing/PR/Advertising JobsSocial Media JobsDigital Marketing JobsPublic Relations Jobs
- Medical/Healthcare JobsDoctor JobsPsychology JobsPhysiotherapist Jobs
- Operations/Management JobsProject Manager JobsMarketing Manager JobsFinancial Manager Jobs
- Pharmaceutical JobsMedical Representative JobsPharmacist JobsRegulatory Affairs Jobs
- Quality JobsQuality Control JobsQuality Assurance JobsHSE Jobs
- Sales/Retail JobsSales Manager JobsAccount Manager JobsTelesales Jobs
- Tourism/Travel JobsTicketing Agent JobsTravel Consultant JobsReservation Agent Jobs
- Writing/Editorial JobsTranslation JobsContent Creator JobsTechnical Writer Jobs
- Analyst/Research Jobs
- Banking Jobs
- Business Development Jobs
- Engineering - Oil & Gas/Energy Jobs
- Fashion Jobs
- Manufacturing/Production Jobs
- Media/Journalism/Publishing Jobs
- Part Time Jobs
- Project/Program Management Jobs
- Purchasing/Procurement Jobs
- R&D/Science Jobs
- Sports and Leisure Jobs
- Startup Jobs
- Strategy/Consulting Jobs
- Training/Instructor Jobs
- Search all jobs
Browse Jobs By Location
- Jobs In Dubai
- Jobs In Sharqia
- Jobs In Riyadh
- Jobs In Monufya
- Jobs In Qalubia
- Jobs In Red Sea
- Jobs In Dakahlia
- Jobs In Suez
- Jobs In Gharbia
- Jobs In Beheira
- Jobs In Jeddah
- Jobs In Beni Suef
- Jobs In Assiut
- Jobs In Matruh
- Jobs In South Sinai
- Jobs In Port Said
- Jobs In Makkah
- Jobs In Damietta
- Jobs In Ismailia
- Jobs In Minya
- Jobs In Abu Dhabi
- Jobs In Fayoum
- Jobs In New Cairo
- Jobs In Maadi
- Jobs In 6th of October
- Jobs In Nasr City
- Jobs In Heliopolis
- Jobs In Sheikh Zayed
- Jobs In Sheraton
- Jobs In 10th of Ramadan City
- Jobs In Obour City
- Jobs In Dokki
- Jobs In Mohandessin
- Jobs In 10th of Ramadan City
- Jobs In Badr City
- Jobs In Mokattam
- Jobs In Shorouk City
- Jobs In Alsadat City
- Jobs In Haram
- Jobs In Helwan
- Jobs In Smouha
- Jobs In Katameya
- Jobs In Downtown
- Jobs In Bourj Alarab
- Jobs In New Nozha
- Jobs In Abu Rawash
- Jobs In Mansoura
- Jobs in Saudi Arabia